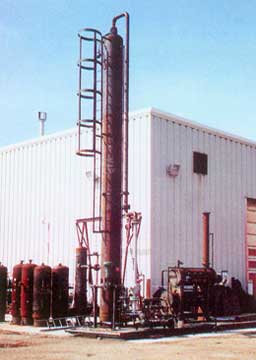
A dehydrator is a device that is used to remove water and water vapour from gas.
FABRICATION:
We currently build and package a range of Dehydration Facilities made to order:
- 12-3/4” through 24” O.D. x 28’-0” S/S
- 1440 PSIG DP at 130 °F
- 3 Phase integral Scrubber
- Welded-in Bubble Cap Tray Systems
- Combined with 125,000 through 250,000 BTU/HR Re-boilers
CUSTOM DEHYDRATORS
We can custom build and package dehydrators to a customer’s specifications.
Dehydration Process
General
A natural gas stream can be dehydrated by contacting the gas with glycol. This process is normally carried out at an elevated pressure in a vessel called a contactor or absorber. After absorbing the water, the glycol is reconcentrated by boiling off the water at atmospheric pressure in a regenerator. A pump is used to recirculate the glycol to the contactor.
Inlet Scrubber
An inlet scrubber is required, either integral with the contactor or as a separate vessel upstream, to remove free liquids from the gas stream going to the contactor. The mist extractor in this vessel removes larger droplets entrained in the gas.
Contactor
The contactor vessels may be categorized as to the manner in which the absorption process is accomplished. One type uses trays equipped with bubble caps, valves, other devices, to maximize gas-to-glycol contact. The action of the gas flowing upward through the glycol layer on each tray creates a froth above the tray, where most of the absorption takes place. The other type of contactor is referred to as a packed tower. It is filled with packing, which has a large surface area per unit volume. Glycol flowing downward wets the entire packing surface. Absorption takes place as the gas flows upward through the packing, contacting the wetted surface. In either type of vessel, a mist extractor removed entrained glycol droplets from the dehydrated gas stream before it leaves the top of the contactor. On larger units, an optional residue gas scrubber may be justified. Rich (wet) glycol is directed from the bottom of the contactor to the regeneration system.
Gas/Glycol Heat Exchanger
Absorption is improved with lower temperature glycol. A gas/glycol heat exchanger is required, which uses dehydrated gas to cool the lean (dry) glycol before it enters the top of the contactor.
Regeneration System
The regeneration system consists of several pieces of equipment. If glycol-gas powered pumps are installed, energy from the high-pressure, rich glycol, along with a small amount of gas, is used to pump the lean glycol. If an optional reflux coil in the still column is provided, the rich glycol flows through it before entering the glycol/glycol heat exchanger. The glycol/glycol heat exchanger serves two purposes:
-
To cool the lean glycol to a temperature as recommended by the pump manufacturer.
- To conserve energy by reducing the heat duty in the reboiler.
Gas-Condensate-Glycol Separator
A frequently used option in regeneration systems is a gas-condensate-glycol separator, which should be included when the inlet gas contains condensate. It may be located upstream or downstream of the glycol/glycol heat exchanger and usually operates at a pressure of 25-75 PSIG. It removes condensate from the glycol prior to the reboiler, which minimizes coking and foaming problems. The separator also captures flash gas that is liberated from the glycol and exhaust gas from the glycol-gas powered pumps so that the gas may be used as fuel. Glycol is regulated from the separator to the reboiler by means of a level controller and dump valve. Condensate removal may be controlled automatically or manually.
Reboiler
Rich glycol enters the reboiler through the still column. It is then heated to 350-400°F, which causes the water that was absorbed in the contactor to vaporize. The reboiler is usually heated by combustion of natural gas, but may utilize other fuels, steam, hot oil or other heat sources. The regenerated lean glycol gravity feeds from the reboiler, through the glycol/glycol heat exchanger and into the pump suction for recirculation back to the contactor. Either electric, gas-powered, or glycol-gas powered pumps may be used.
Still Column
Water and glycol vapours from the reboiler enter the bottom of the still column, which is mounted on top of the reboiler. The bottom section contains packing, while the top section of the still column may contain a reflux coil or external fins. Reboiler vapours are cooled and partially condensed to provide reflux, which improves the separation between glycol and water. The remaining water vapour leaves the top of the still column and vents into the atmosphere.
Filters and Strainers
Regeneration systems contain various types of filters and strainers. A particle filter or fine mesh strainer is required to protect the pump. To reduce foaming, an activated carbon filter may be installed to remove heavy hydrocarbons from the glycol. There is no standard arrangement for these items in the system.