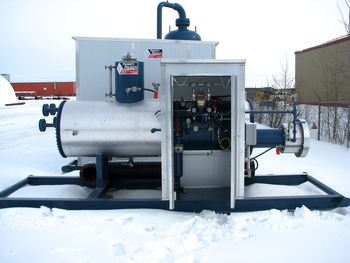
Line Heaters are used to help maintain an optimal temperature in the well stream as pressures are reduced. They counteract abrupt temperature drops that happen when the well stream passes through the choke and are reduced in pressure. They can also be used to heat gas transmission lines.
Fabrication:
Heater Coils are fabricated to ANSI Code B31.3 for either sweet or sour service.
All Heaters are equipped w/ Burner Management System (BMS) in compliance w/ B149.3
Inventory:
We maintain an inventory of new and reconditioned Line Heaters, for both sweet and sour service, with capacities ranging from 500,00 BTU/HR through 1,000,000 BTU/HR. All equipment inventory is available for Sale, Rent or Rental Purchase.
What Is a Line Heater?
The indirect oil & gas line heater is a specialized equipment used in the oil and gas industry to heat fluids, such as crude oil, natural gas, and other hydrocarbons, as they flow through pipelines. It is designed to maintain the temperature of the fluid above its pour point or to a specific temperature required for transportation, processing, or storage.
The basic working principle of an indirect oil & gas line heater involves using a heat transfer medium to indirectly heat the fluid inside the pipeline. The most common heat transfer medium used is a thermal oil or a glycol solution, which is heated by a separate heating source, such as a burner or an electric heater.
The process of how an indirect oil & gas line heater works can be summarized in the following steps:
-
Heat Generation: The heat transfer medium, either thermal oil or glycol solution, is heated by a burner or an electric heater in a heat exchanger. The burner or electric heater provides the necessary heat energy to raise the temperature of the heat transfer medium to the desired level.
-
Heat Transfer: The heated heat transfer medium is then circulated through a closed-loop system, which typically includes a pump and a network of pipes or coils, that is in contact with the pipeline carrying the fluid to be heated. As the hot heat transfer medium flows through the pipes or coils, it transfers its heat to the fluid inside the pipeline through the walls of the pipes or coils, indirectly heating the fluid.
-
Temperature Control: The temperature of the fluid inside the pipeline is controlled by monitoring the temperature of the heat transfer medium and adjusting the heat input from the burner or electric heater accordingly. This ensures that the fluid inside the pipeline is heated to the desired temperature and maintained at that temperature during transportation, processing, or storage.
-
Safety Measures: Indirect oil & gas line heaters are typically equipped with safety features, such as pressure relief valves, temperature sensors, and automatic shut-off systems, to ensure safe and efficient operation. These safety measures help prevent over-heating, pressure build-up, and other potential hazards.
-
Energy Efficiency: Indirect oil & gas line heaters are designed to be energy-efficient, as they use a closed-loop system for heat transfer, which minimizes heat loss to the environment. Additionally, modern indirect line heaters often utilize advanced control systems and insulation materials to further improve their energy efficiency and reduce operating costs.
In summary, the indirect oil & gas line heater uses a heat transfer medium, such as thermal oil or glycol solution, to indirectly heat the fluid inside a pipeline through a closed-loop system. It relies on heat generation, heat transfer, temperature control, safety measures, and energy efficiency to ensure effective and efficient heating of the fluid during transportation, processing, or storage in the oil and gas industry.
Contact Priority Projects For Any Line Heater Sizing, Design, Installation, Maintenance & Repairs
Priority Projects for 40 years has been providing high-quality fabrication and equipment rental services, offering experience serving the energy industry. You can rest easy with our reliable products to prevent hydrates from forming in pipelines, thus eliminating expensive downtime.
If you are looking for more information, reach to out our line heater equipment experts by calling 1-780-955-3320 . You can also fill out a contact form if you have any questions.
Line Heater Terminology
Introduction:
Heating of oil and gas streams close to the wellhead is normally done for the purpose of preventing hydrate or wax formation. Wellstream heating may also be done to prevent liquids from condensing in the gathering line or to facilitate subsequent fluid separations.
An indirect type oil field heater employs a water solution, maintained below the boiling point, as the heating medium for the purpose of heating the process fluids in the coils.
Line Heater Components:
- Burner System: Firing the heater requires a burner system designed for the specific fuel to be used and may be either natural or forced draft design. The burner system includes the firing accessories, intake flame arrestors and other optional burner accessories.
- Choke: A device to restrict and control the flow rate of well fluids. It may have a positive fixed orifice with removable bean or an adjustable variable orifice. The choke may be located upstream of the oil, between passes in the coil bundle, or on the coil outlet. A submerged or long nose choke may be used with pressure reduction taking place within the water bath to minimize hydrate formation.
- Coil Area: The coil area is the heat transfer area and is normally calculated using the outside surface area of the pipe.
- Coils: The fluid to be heated is passed through one or more coils, which may be typically arranged as a single pass coil or split pass coil. The coil may also be referred to as a tube bundle. The single pass coil normally has only one flow path. The split pass coil may be designed for two pressure ratings, allowing for a choke to be located between the two coil sections. Split pass coils are used when it is necessary to use two heating stages to minimize hydrate formation within the coil. Multiple coils may be used if more than one well stream is processed in the same heater shell.
- Fill Connection: This connection on the top of the shell shall be provided with a pressure-vacuum venting device. If a water saver is furnished, the fill and vent connection may be integral with it.
- Firebox: A complete assembly consisting of the tube, mounting flange, intake and stack adaptors.
- Firetube: Natural gas is normally used to fire the heater through a submerged furnace chamber called the firetube. The firetube normally consists of one or more U-tubes fired at one end and exhausting through a vertical stack for each U-tube. The firetube is that portion of the firebox in contact with the heater bath.
- Heater Bath: The indirect heating medium is referred to as the heater bath and within the scope of this specification the heater bath is limited to water or water solutions. When freezing is possible, ethylene glycol may be added for anti-freeze protection. Other additives to the water bath may include corrosion inhibitors.
- Heat Density: This term is commonly applied to the heat release through the cross section of the firetube, expressed as BTU/hour/square foot of exposed area.
- Intake Flame Arrestor: A device placed on the air intake of the firetube to prevent propagation of flame from inside the firetube to the outside atmosphere. It normally consists of a corrugated aluminum cell mounted in a metal housing, which attaches to the firebox.
- Stack Downdraft Diverter: A device attached to the top of the stack designed to reduce the effects of wind currents on the burner system.
- Stack Flame Arrestor: A device attached to the top of the stack designed to reduce the effects of wind currents on the burner system.
- Stack Rain Shield: A device attached to the top of the stack to prevent rain from falling directly into the stack. It may also serve as a stack downdraft diverter.
- Water Saver: A chamber may be directly connected to the heater shell to permit the shell to be completely filled with water. The water in this chamber exists at a lower temperature than the heater bath, which reduced evaporation losses. It may also be referred to as an economizer or expansion tank. Its capacity should be sufficient to contain the water expansion between ambient and operating temperatures.